Actuator information
Type: | Indirect injection |
---|---|
Power supply: | 12 V from system relay |
Signal type: | Frequency and duty cycle varying |
Signal level: | 0 A to 1 A |
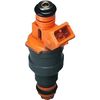
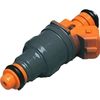
Workings of an injector
An injector sprays pressurized fuel into the inlet system or a cylinder. Due to the small opening in the injector and the high pressure, the fuel is atomized when it leaves the nozzle.
The particular injector measured for this article contains a metal pin that is kept pushed against a small opening by a spring. A coil is placed around the metal pin. A strong enough current flowing though the coil generates a magnetic field lifting the pin off the seat, opening the injector. While the current remains, the injector is held open. When the current is interrupted, the spring pressure pushes the metal pin back to its original position, closing the opening.
In most cases the injector has a power supply from a system relay and a switched ground wire connected to the ECU. In some cases the ECU controls the positive injector side and the negative side is permanently connected to ground.
A mono point injection system uses one injector placed just in front of the throttle valve. A multi point injection system uses one injector per cylinder placed in the inlet manifold just in front of the inlet port of a cylinder.
The injection moment is determined by the ECU according to the engine position which is determined from the crankshaft sensor signal and optionally the camshaft sensor signal. The ECU determines the injector's opening duration mainly from the engine temperature and demanded power.
Connecting the lab scope
Correct functioning of the injector can be checked by measuring the following signals, see figure 1:
Channel | Probe | Voltage | Range |
---|---|---|---|
1 | ![]() |
Signal voltage at injector | 80 V |
![]() |
Ground at battery | ||
2 | ![]() |
Current clamp positive connection | 200 mV |
![]() |
Current clamp negative connection |
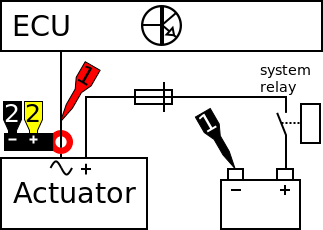
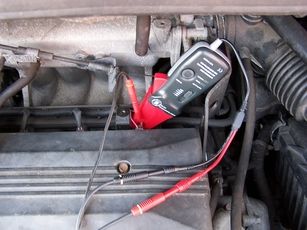
Channel 1 of the lab scope is connected to the injector via a Measure lead TP-C1812B and Back Probe TP-BP85. The current is measured with a Current clamp TP-CC80 which is connected to channel 2 of the lab scope with the use of a Measure lead TP-C1812B. The Current clamp TP-CC80 is set to the 20 ADC range and outputs a voltage of 100 mV per 1 A. To get a readout in Ampères, the current clamp's signal voltage has to be amplified 10 times. This can be done via the menu item "probe settings" in the right click menu of channel 2. In that same menu the "Set unit..." can be used to change the unit to 'A'. The lab scope is set to normal scope mode.
Measuring
Figure 3 shows injector voltage and current waveforms of an idling engine at operating temperature. This signal can be downloaded and used to correctly set up the lab scope or as reference signal.
Download indirect injection current measurement
Channel 1 (red) shows the signal voltage of the injector about which more information can be found in the injector voltage measurement. Channel 2 (yellow) shows the current through the injector. When injector is activated by the ECU at t=0, the signal voltage drops and a current starts flowing. The current builds up a magnetic field which, when strong enough to overcome the spring pressure, lifts the pin from the seat and opens the injector. The movement of the pin through the magnetic field is visible in the current signal, see figure 3.
When the injector has been open long enough, the circuit is interrupted by the ECU at t = 3.92 ms. At this time the current is peaking at about 1 A. Because the circuit is interrupted, the current stops immediately. The built up magnetic field slowly decreases until it is too weak to overcome the spring force, which then pushes the pin back on its seat. The movement of the metal pin changes the magnetic field which in turn affects the signal voltage. This is visible as a small hump in the signal.
Vertical cursors are used to indicate the injector's opening and closing moment. This shows that the injector has been open for a little over 2 ms.
Diagnosis
Signal values may differ on different types of engine control units and injectors. Consult ATIS for information on specific engine control units and injectors.
The following signal deviations can indicate a problem:
-
No signal:
Cause: back probes have no connection (perform a connection test), current clamp isn't switched on or has a empty battery, no power supply, amplifier of ECU defective, injector defective -
Signal voltage too high
Cause: current clamp was not properly zeroed -
Noisy signal:
Cause: power supply or signal wires damaged, poor connection in connector terminals, injector defective -
Signal shows an offset in relation to example signal:
Cause: current clamp was not properly zeroed
RELATED PRODUCTS
RELATED ARTICLES
- Indirect injection voltage measurement
- A lab scope is used to measure an injector signal voltage on an idling engine at operating temperature. The signal from the sensor is shown and can be downloaded. To help determining whether the injector is functioning correctly, different possible deviations from the example signal are mentioned along with possible causes.
- Toyota MR2 bad injector
- A Toyota MR2 is having problems after an engine replacement, fault code P0304 Cylinder #4 misfire detected occurs. The garage swaps several components but does not manage to fix the problem. Measurements with an automotive oscilloscope are required to find out that the fault code is somewhat misleading and the problem is not with cylinder #4
This document is subject to changes without notification. All rights reserved.
The information in this application note is carefully checked and is considered to be reliable, however TiePie engineering assumes no responsibility for any inaccuracies.
Safety warning:
- Before measuring, check that sources of dangerously high voltages are switched off or shielded from contact. Voltages considered to be dangerous are voltages over 30 V AC RMS, 42 V AC peak or 60 V DC.
- Keep a clean working environment when doing measurements.
- This measurement and procedures are a examples / measuring suggestions and are no prescribed protocols.
- TiePie engineering can not anticipate the safety actions that need to be taken to protect persons and appliances. Before starting a measurement, check which safety measures need to be applied.